Blog
Service tickets for machine maintenance: Optimize with tapio
Thursday, April 17, 2025
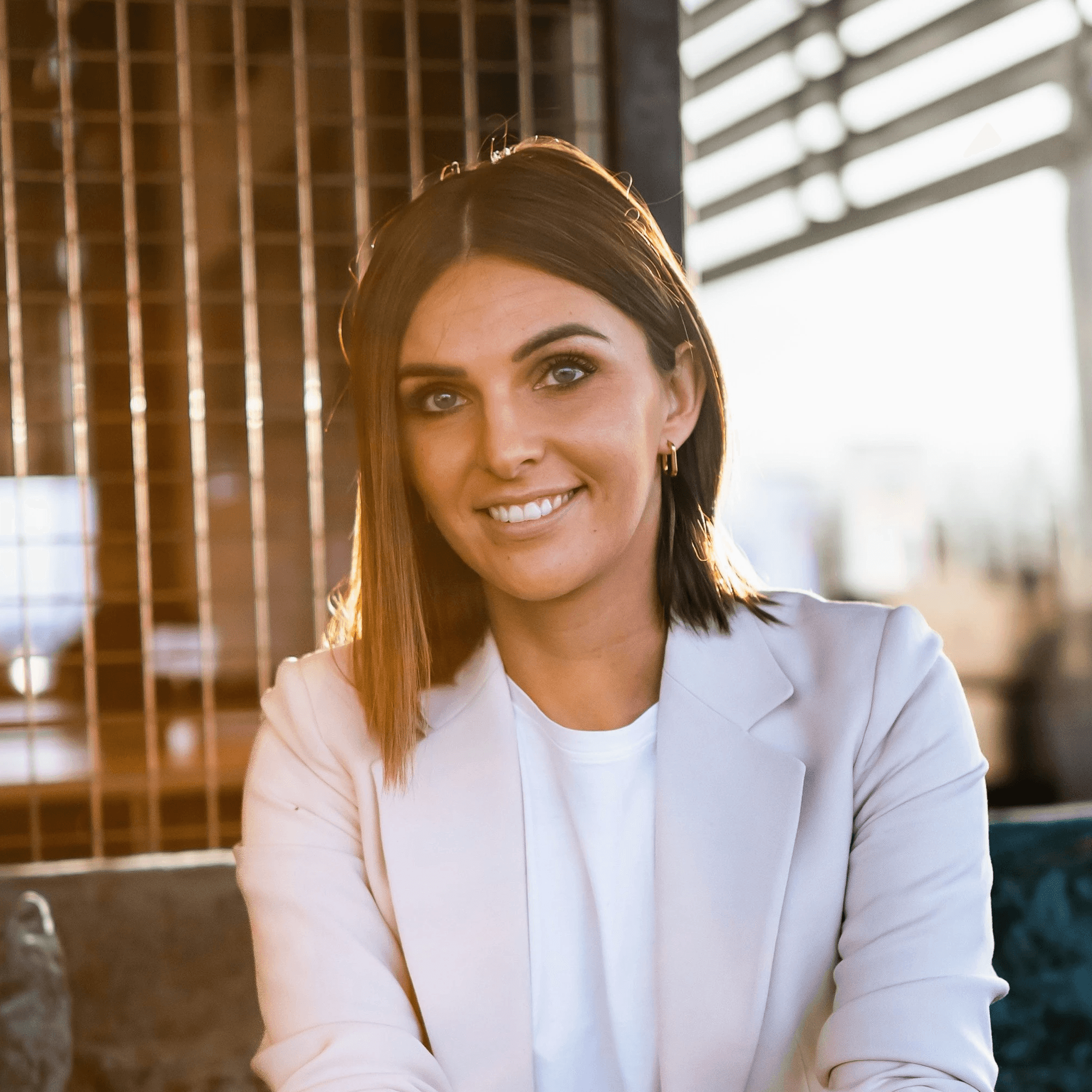
Cathjana Seeger
Every carpentry relies on powerful machines. However, if a CNC milling machine, an edge-banding machine, or a panel saw fails and stands still, it can become expensive.
The solution? Digital service ticket systems for machine maintenance. Such a system ensures that errors are reported, documented, and resolved faster – and with minimal effort. Instead of struggling to find the right contact person, making phone calls, and enduring long wait times, carpenters can manage service cases digitally and systematically.
Table of Contents
What are digital service ticket systems for machine maintenance?
The tapio ServiceBoard: Your digital service ticket system for machine maintenance
The challenges of traditional machine maintenance
Many carpentries know the problem:
Lack of transparency: No one knows exactly if, when, and by whom the problem was reported.
Cumbersome error documentation: Notes on paper get lost, photos of damages end up in confusing WhatsApp groups.
Long communication pathways: Calls with technicians are often time-consuming and ineffective.
High downtimes: While waiting for service intervention, production stands still.
These challenges can be efficiently solved with a digital service ticket system for machine maintenance.
What are digital service ticket systems for machine maintenance?
A digital service ticket system helps manage service cases efficiently. It allows:
Digital error reporting – No more lost notes.
Uploading photos & videos – Visual documentation facilitates error analysis.
Automatic forwarding to the right technician – No misunderstandings.
All service cases in one place – Traceable service history.
These systems ensure that carpenters and machine manufacturers communicate faster and find solutions – without unnecessary wait times.
The tapio ServiceBoard: Your digital service ticket system for machine maintenance
With the tapio ServiceBoard, carpentries have a powerful solution at hand to optimally manage service cases.
Create service tickets with photos and videos – Precisely document errors.
Direct communication with service technicians – No more lengthy queues.
Utilize video diagnostics – Analyze machine problems via live video.
Central documentation of all service cases – Every maintenance remains traceable.
Practical example:
A carpenter notices a malfunction on his HOMAG CNC machine. Instead of searching for the error for a long time, he creates a service ticket in the ServiceBoard in just a few seconds, takes a photo, and sends it directly to technical support. Thanks to clear documentation, the technician can immediately narrow down the problem – without long guessing.
Comparison: ServiceBoard vs. traditional service processes
Feature | Traditional Service | ServiceBoard |
---|---|---|
Error documentation | Handwritten, often illegible | Digital, with photos and videos |
Communication | Long phone calls with many follow-up questions | Direct contact with technicians |
Error resolution | Time-consuming due to unclear information | Fast, precise error analysis |
Downtime | High, as problems remain unresolved for long | Shorter, as technicians react quickly |
With the tapio ServiceBoard, carpenters not only save time but also costs for unnecessary machine downtimes.
Like many other apps from the tapio app world, the ServiceBoard allows the integration of additional partners. Talk to your service partner about it or become a partner in ServiceBoard!
Best practices for digital machine service
Use one channel consistently – Every service case should be submitted through the ticket system.
Use photos and videos – Technicians can better analyze problems this way.
Train employees – Everyone in the workshop should know how to use the ServiceBoard.
Use video diagnostics – Often, problems can be solved remotely without a technician on site.
Conclusion
Digital service ticket systems for machine maintenance are the future – and the tapio ServiceBoard offers carpenters an optimal solution. It reduces downtime, improves error documentation, and simplifies communication with technicians.